5 Innovations in Casting Technology Every Supplier Should Adopt
In today’s fast-evolving manufacturing industry, staying ahead of the curve is essential for every casting supplier aiming to deliver high-quality components, meet tighter tolerances, and reduce lead times. As industries like automotive, aerospace, and heavy machinery demand more precision and customization, casting technology has undergone significant transformations. To remain competitive and future-ready, a casting supplier must embrace the latest advancements that not only improve productivity but also ensure better cost-efficiency and environmental sustainability.
In this blog, we’ll explore the five most important innovations in casting technology that every casting supplier should consider adopting to enhance performance, client satisfaction, and market relevance.
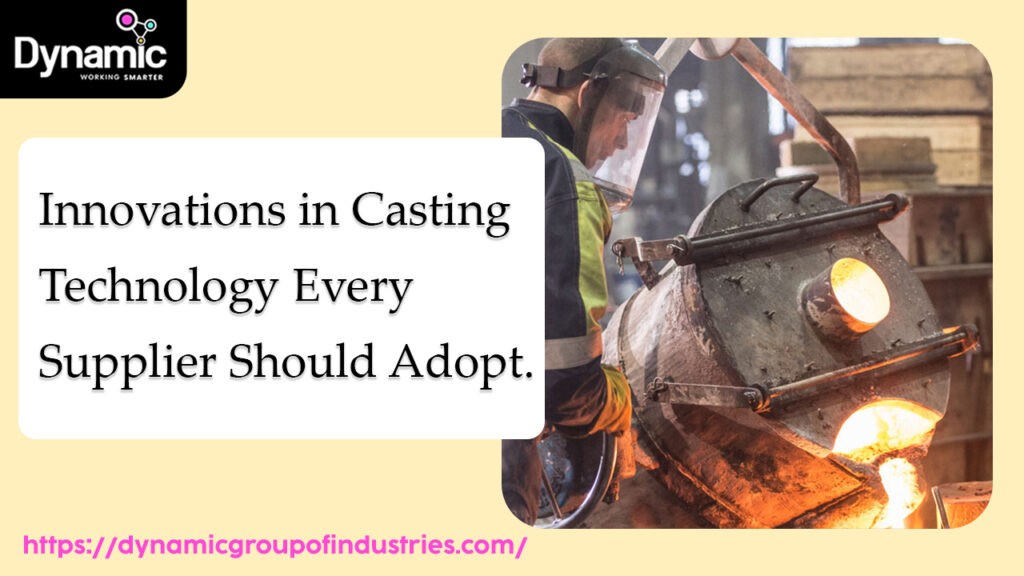
3D Printing & Rapid Prototyping in Casting
Revolutionizing Mold Making
Additive manufacturing, commonly known as 3D printing, has changed the way molds and patterns are developed in casting. Traditional mold-making processes are often time-consuming and expensive. But with 3D printing, a casting supplier can produce complex and customized molds in a fraction of the time, improving turnaround and reducing material waste.
Benefits:
- Faster design-to-production timelines
- Customization for low-volume or one-off parts
- Reduced tooling costs
Real-World Application:
Investment casting now commonly incorporates 3D printed wax patterns, which help in producing intricate geometries that were previously impossible with conventional methods.
Simulation Software for Defect Prediction
Enhancing Quality Control
Modern simulation tools such as MAGMASOFT, ProCAST, and AnyCasting allow casting suppliers to simulate the flow of molten metal, solidification behavior, and cooling processes — before actual production begins. These tools help in predicting defects like porosity, shrinkage, and hot spots, enabling adjustments in gating design or cooling rates without trial and error.
Benefits:
- Improved first-time quality (FTQ)
- Reduced rejection rates
- Data-driven decision making
Why It Matters:
Casting suppliers who use simulation tools are more likely to deliver defect-free products, enhancing customer trust and long-term partnerships.
Automation & Robotics in Casting Operations
Increasing Efficiency and Safety
The integration of robotics and automation in core making, mold handling, pouring, and fettling operations has brought significant gains in consistency and workplace safety. Robots can perform repetitive tasks like cleaning and grinding with high precision and less fatigue compared to manual labor.
Benefits:
- Consistent product quality
- Improved workplace safety
- Increased productivity and throughput
Case Example:
A leading casting supplier in Germany implemented robotic pouring systems, resulting in a 25% increase in casting accuracy and a 40% reduction in manpower dependency in high-temperature zones.
Advanced Alloys and Material Innovation
Catering to New Industry Demands
The demand for lightweight, high-strength materials has led to the development of advanced alloys such as aluminum-lithium, titanium-based alloys, and metal matrix composites. These materials are essential for industries like aerospace and electric vehicles, where weight-to-strength ratios are critical.
Benefits:
- Lightweight components without compromising strength
- Higher corrosion and wear resistance
- Compatibility with precision casting techniques
What It Means for Casting Suppliers:
A forward-thinking casting supplier must invest in R&D and infrastructure to handle advanced materials and develop proprietary alloy blends that meet specific customer needs.
Sustainable & Eco-Friendly Casting Methods
Reducing Environmental Footprint
Sustainability is no longer an option—it’s a necessity. Innovations like closed-loop sand reclamation, reduced energy furnaces, and low-emission binders have helped many casting suppliers minimize their environmental impact.
Benefits:
- Lower energy consumption
- Reduced raw material waste
- Compliance with global environmental regulations
Green Certifications:
A casting supplier that implements eco-friendly practices can earn green certifications like ISO 14001, which enhances brand reputation and attracts environmentally conscious clients.
Why Innovation Matters for a Casting Supplier
To summarize, here’s why these innovations are critical for every casting supplier:
- Customer Expectations Are Rising: Clients want high-precision, defect-free components delivered faster than ever.
- Global competition is fierce: Suppliers that fail to innovate risk being replaced by more tech-savvy competitors.
- Regulations Are Tightening: Environmental and quality standards are growing stricter globally, especially in automotive and aerospace sectors.
How to Get Started
If you’re a casting supplier looking to implement these innovations, start by assessing your current capabilities and identifying the most critical areas for improvement. Partnering with industry experts, attending global foundry expos, and investing in skilled talent are some great ways to begin your transformation.
Conclusion
Innovation in casting is not a luxury—it’s a survival strategy. From 3D printing and simulation to sustainable practices, each advancement discussed here can help a casting supplier improve quality, reduce lead times, and future-proof their business. Adopting even one of these technologies can make a significant difference in operational efficiency and customer satisfaction.
Are you a casting supplier looking to level up your operations? Embrace these game-changing innovations and lead the way into the future of manufacturing.